Improving Manufacturing Performance with a Few Simple Numbers
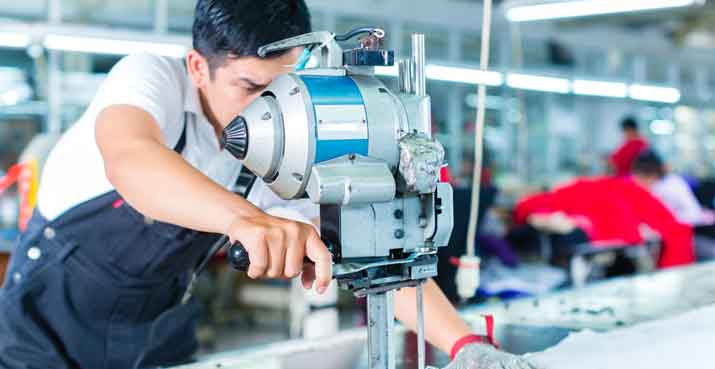
Business leaders are constantly in search of data regarding their business. Manufacturing professionals especially value so-called “hard” business data as a means of completely understanding and separating profitable operations from unprofitable ones. In today’s Information Age, discover more, there seem to be as many different ways of measuring manufacturing performance as there are types of equipment in the manufacturing industry.
Efforts to measure what a machine or work center is doing, however, sometimes obscure what is not being done, lost opportunity that if corrected would yield significant returns and may only require little investment. But how can “lost opportunity” be measured, let alone understood? Fortunately there is one metric that concisely and easily communicates multiple opportunities in a comprehensive manner – OEE.
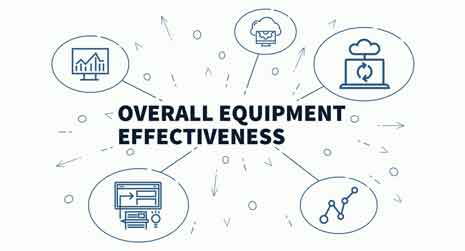
OEE is an acronym for Overall Equipment Effectiveness. OEE is expressed as a percentage, with 0% representing no effectiveness and 100% the equivalent of manufacturing perfection. The OEE calculation is the product of three other percentages – one each for Availability, Performance, and Quality. The formula
can be written like this:
(A%) x (P%) x (Q%) = OEE%
Implemented properly, OEE is an ideal indicator of an area’s current work rate compared to its absolute potential and drives focus to the areas of greatest opportunity. Understanding and implementing OEE requires a thorough understanding of its three basic elements.
Availability: Work center Availability essentially measures the amount of time the machine was in use, compared to the time it should have been in use. An important (and somewhat confusing) component of Availability is Net Operating Time. What is Net Operating Time? It is the time left after subtracting
all the time when work will NOT be scheduled: Holidays, planned shutdown periods, weekends, etc. All time within a calendar year when work is scheduled equals Net Operating Time. On a weekly basis, this may be 120 hours (24 hours x 5 days) or 168 hours (24 hours x 7 days). Time not spent producing is tracked and reported as Availability. Typical availability losses include changeover time, preventive maintenance windows, and employee lunch/breaks.
For example, let’s assume we have machine scheduled to work eight hours each shift (Net Operating Time = 8 hours). On a particular shift, the machine is down 30 minutes for a changeover and one hour due to employee lunch/breaks – what is the machine’s Availability? Subtract the losses from the Net Operating
Time (8 – 1.5 = 6.5), then divide by the Net Operating Time (6.5 / 8 = 81.25%).
Performance: Work center performance is the most easily grasped of the three OEE metric components, as many manufacturing managers already measure machine output in some respect. In simple terms, Performance is the percentage of actual parts produced vs. the theoretical parts that should have been produced in the same time-frame. The key difference for most managers is that existing run standards may not be a truly theoretical and are instead “historical”, incorporating downtime and other inefficiencies which skew the data lower than what the machine may actually be capable of producing.
As an example, let’s assume our machine has a standard production rate of 200 units per minute (or 96,000 in 8hrs). How much output should we expect in our Availability example above? If you said 78,000 (200/min. x 60 min/hr x 6.5hrs of operating time), you passed! However, if during our 6.5hr shift the machine was down 45min. for troubleshooting & repair, our output would be reduced further. Let’s say we only produced 61,000 parts for this particular shift. Our Performance calculation would yield 78.2% (61,000 actual / 78,000 theoretical for the 6.5hr run time).
Quality: The Quality component, like the Performance component, is a discrete and is relatively easy to comprehend. Your machine or process is making something, and each “something” is either of acceptable quality (“good”) or not (“bad”). The Quality component of OEE measures the percentage of “good” parts compared to the total number (“good”+”bad”) of parts produced. Many manufacturing facilities heavily scrutinize the output of each work center (the “good” number), but far too few measure or have the ability to measure the volume of rejects.
One last example with our fictional machine: In our Performance example above, the machine only managed to produce 61,000 parts. How many of them were good? Did we assume they were all good? Suppose upon examination only 56,000 parts passed inspection. Our Quality rate would then equal 91.8% (56,000 good / 61,000 total).
As stated earlier, OEE is the product of Availability, Performance, and Quality. So, now that we have example data, let’s calculate the OEE of our machine during the shift in question:
OEE = (81.25%) x (78.2%) x (91.8%) = 58.3%
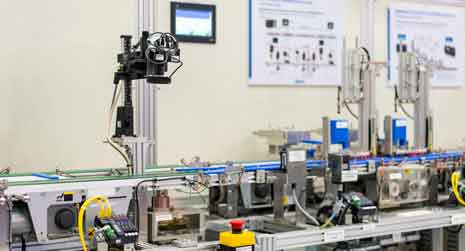
Okay, so what does 58.3% mean? Basically it means we are losing over two-fifths of our machine’s ability to produce. More importantly, we know where these losses are occurring, so we can investigate these areas further, find out why and take action to improve them. Best of all, we will be able to see (through continued OEE monitoring) the impact our actions have on the machine.
Through a few simple measurements, OEE can quickly bring to light a work center’s true performance capability, highlight opportunities for improvement, and over time measure the impact of changes.