How to Use End Mills
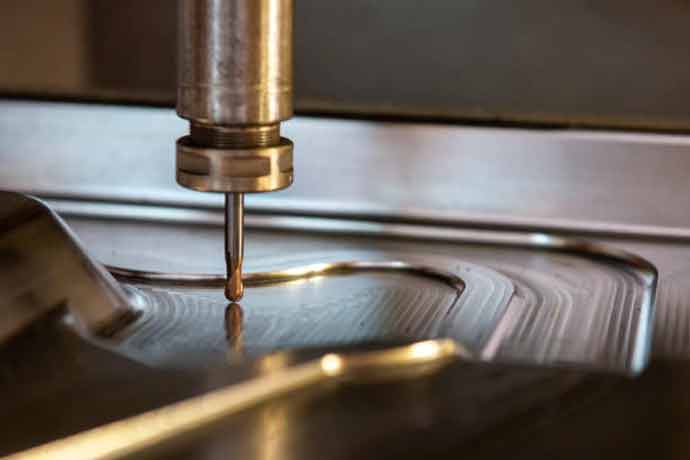
Before you start using an end mill, you should understand how it works. There are several things to keep in mind when using one, including the number of flutes and the material that you are cutting. Once you know this information, you will have a much easier time using an end mill to cut different materials.
Choosing the right end mill
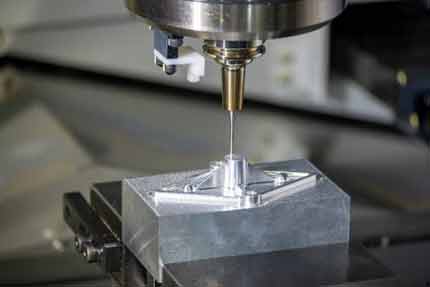
Choosing the right end mill is critical to achieving the desired finished product. There are several factors to consider, including material properties, tooling geometries, and cutting speeds. Using an end mill guide can help you select the right tool for your application. The endmill selection guide will also provide technical information about various endmill features, such as feed rates, chip load per tooth, and feed per revolution.
Different end mills are designed for different applications, such as producing lateral cuts, tracing, drilling, and slotting. Choosing the right end mill is important to achieving the desired surface finish and ensuring that your project is successful. Incorrect selection can damage your work piece, which costs you time and money.
Choosing the number of flutes
Selecting the right end mill for a specific material is a critical step in manufacturing. The material will affect the performance of the end mill as well as the finish quality. If you choose the wrong mill, you risk breaking the tool or damaging the workpiece. To help reduce the risk of broken tools, choose the appropriate mill with a proper number of flutes.
The number of flutes on an end mill depends on the material and machining process. For example, if you are working with aluminum, a 2-flute end mill is often the most appropriate choice. However, if you’re working with steel, you may want to use a high-flutes end mill. This will allow for increased strength and reduce tool wear. Higher-flutes also produce a smoother finish.
Calculating feed rate
When using an end mill, the feed rate should be calculated based on the material that you’re milling. The slower the feed rate, the smoother the workpiece finish. You can use a feed rate calculator to help you calculate the proper feed rate. It will also tell you the minimum and maximum speed for the milling operation.
In general, the feed rate is defined in inches per tooth. However, the feed rate varies depending on the tool’s diameter and the work material. In calculating feed rate, you need to consider the following factors: Surface Speed, Chip Load, and Work Material. If you’re milling plywood, the chip load should be around 0.17mm per tooth, Browse around this site.
Choosing the right material
Choosing the right material for an end mill is an essential step in the process of milling. The process of milling is usually divided into three phases, roughing, semi-finishing, and finishing. The right material for each of these phases is dependent on the application. Usually, the diameter, cutting edge length, and flute length must be chosen according to the type of application. The rule of thumb is to go for the shortest end mill with the largest diameter.
Conclusion:
The type of end mill you use is crucial for the quality of the finished product. You should choose a high-quality 2-flute end mill for milling hardwoods, plywood, or aluminium. When choosing the right tooling, you should remember to match the feed rate to the end mill’s optimal speed. In some cases, you may be able to reduce the operating speed by as much as 50%, which will significantly increase the life of the tool. In addition, you must ensure that proper chip evacuation is done during the process. If you fail to do this, you may end up with a poor-quality cut.