A 3D Printed Titanium Jawbone Transplant
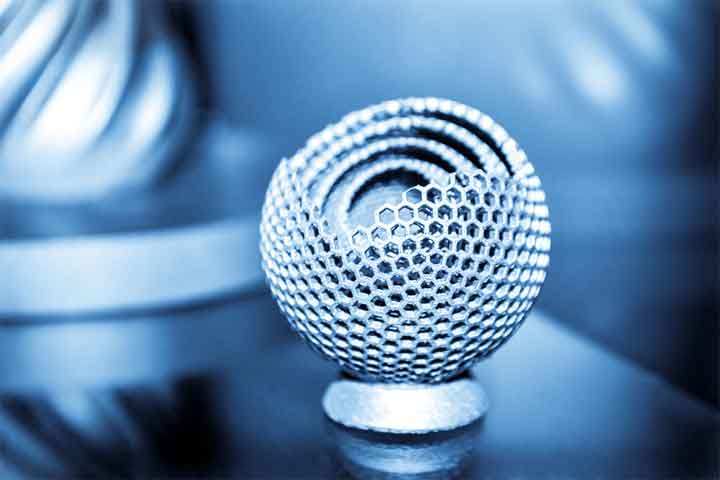
One thing about working in technical services for a large company is that I got to see and experiment with some fairly advanced technology. I was in charge of maintaining and improving engraving and printing equipment primarily in a rotogravure print setting though we also did some offset printing. 3D printing is something I investigated for making print cylinders and plates. As I learned more about 3D printing I discovered we could easily use the technology to fabricate intricately shaped parts for our specialized equipment.
A 3D printer can produce a single part at far less cost than traditional methods which often required months in lead time and thousands of dollars for design, sand casting and machining. I could design a worn or broken part with 3D CAD and print out the part or contract the work to a business with more suitable equipment. If we view the human body as a very fine biological machine then it is easy to consider printing a replacement body part. An 83 year old woman recently had her lower jawbone replaced by a specially printed titanium replacement. This is how it was done and what we can look for in the future.
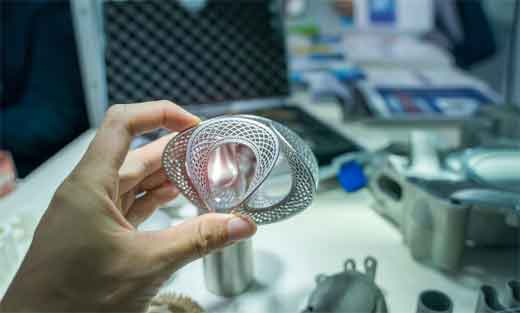
The problem
The elderly woman had an infection of the lower jawbone that did not respond well to treatment and had to be removed. Traditional microsurgical reconstruction wasn’t considered feasible due to her age. It was decided to replace the entire lower jawbone with a 3D printed replacement. The project was a joint effort between the University of Hasselt, Belgium, several other colleges, Xilloc Medical BV, The Netherlands (3D design), and Layerwise, Belgium, who did the actual additive printing. You can get more details on the participants and procedure here.
The solution
The replacement jawbone is designed to mesh perfectly with existing bone structure. The information available doesn’t specify but I’m assuming CT scans were used to achieve correct dimensions and shape. Such scans have been used to make models which help surgeons better prepare for delicate surgical repairs. Titanium powder was printed at 33 layers per millimeter and precision fused by laser. The titanium jawbone has holes and grooves to guide regrowth of muscles, nerves and veins. The finished implant was coated with artificial bone (bioceramic) by plasma spray application. I find the plasma application especially interesting because it is exactly the same method we used to treat certain drive cylinders for paper web handling equipment.
The outcome
The custom fit implant allowed for shorter surgery time. Within hours the woman was able to speak and swallow and had natural jaw movement. After four days the woman was able to leave the hospital. A future procedure will add teeth. The implant is slightly heavier than the original bone structure but should cause no problems.
The future
There has been limited application of 3D printed body parts, mostly partial implants. The transplant of a full bottom jawbone opens up more possibilities for the future. There is even some interest in printing human tissue and organs. All you need is the right “ink.” My body is wearing out. I think I’ll volunteer.